“禁油令”还是 “限油令”?一字之差、谬以千里
全球涂料网讯:
17防腐蚀涂料年会已于5月15-18日在深圳成功召开,来自原材料、涂料生产、设计单位、科研院所、业主等超过三百人参加了此次年会,同时年会也邀请到中科院、中石油、中石化、中海油、中船重工、中集、振华港机、哈尔滨工业大学、扬州大学、佐敦、海虹、科思创等单位的知名专家针对相关内容发表主题演讲。
此次年会主要分为六大主题两大论坛,分别是:
主题一:中国的腐蚀现状及涂料行业的未来方向;
主题二:水性化时代,提高产品性能、降低涂装要求将是持续关注的话题;
主题三:低成本的绿色转型之路——高固体分、无溶剂专题;
主题四:纳米潮的重演?——石墨烯专题;
主题五:新常态下,海工船舶涂料的突破及出路;
主题六:新技术、新成果暨“道蓬杯”优秀论文评选;
论坛一:水性 or 高固无溶剂化,你怎么看?
论坛二:石墨烯在涂料中的应用现状及未来。
中国化工学会涂料涂装专业委员会作为此次年会的承办单位,将根据年会的主要内容,倾听行业的声音,结合现阶段的相关政策、标准,推出2017防腐蚀涂料年会的系列后续报导,敬请期待!
接下来的文章可能涉及的主题报告
“水性化”“水性涂料”“水漆”“环保水漆”等等名词在近两年基本占据了相关涂料行业媒体的版面头条,是涂料企业宣传、推广的杀手锏,新的基地建设也是以水性涂料生产为主。在此我们不讨论水性建筑涂料及木器涂料,因为我们知道,建筑涂料领域,除防水与地坪,其他已基本实现水性化;水性木器涂料在推广中虽然遇到不少问题,但油性木器涂料转水性和辐射固化涂料的大体方向基本无疑。在此篇文章中,我们主要针对工业防腐涂料进行讨论。
在防腐涂料的转型中,有部分文件是我们需要了解的,它们构成了涂料行业未来发展的政策依据。2015年5月8日,国务院印发《中国制造2025》;2015年9月21日,中共中央、国务院印发了《生态文明体制改革总体方案》,这两个文件都以绿色为重要指导思想。2016年7月8日,为贯彻落实《中国制造2025》和《大气污染防治行动计划》,工信部和财政部联合发布《重点行业挥发性有机物削减行动计划》,总体目标:到2018年,减少苯、甲苯、二甲苯、二甲基甲酰胺(DMF)等溶剂使用量20%以上,低(无)VOCs的绿色涂料产品比例分别达到60%以上。和防腐涂料有关的章节:重点推广水性涂料、粉末涂料、高固体分涂料、无溶剂涂料、辐射固化涂料(UV涂料)等绿色涂料产品。鼓励企业实施生产过程密闭化、连续化、自动化技术改造,建立密闭式负压废气收集系统,并与生产过程同步运行。采取密闭式作业,并配备高效的溶剂回收和废气降解系统。2016年11月24日,国务院印发《“十三五”生态环境保护规划》。到2020年,生态环境质量总体改善。全面推进炼油、石化、工业涂装、印刷等行业挥发性有机物综合整治。涂装行业实施低挥发性有机物含量涂料替代、涂装工艺与设备改进,建设挥发性有机物收集与治理设施。2016年12月7日,国家发改委网站发布公告,对《外商投资产业指导目录》修订稿公开征求意见 。在第十章《化学原料和化学制品制造业》方面规定:鼓励投资高性能涂料,高固体分、无溶剂涂料,水性工业涂料及配套水性树脂生产。2017年2月4日, 国家发改委网站发布《战略性新兴产业重点产品和服务指导目录》2016 版,是落实和引导全社会资源投向的具体举措,进一步细化各个产业中具有市场需求和价值的产品和服务,为企业制定战略方针提供支持。新材料产业领域中的“表面功能材料”内容涵盖了:环境友好型防腐涂料,环境友好型高性能工业涂料,水性重防腐涂料等。
在中央部委层面,明确针对涂料提出了五点绿色化方向,引领涂料企业进行转型升级。在相关中央文件出台后,各地方政府也陆续出台相关规划及方案,以下列举部分。
《江苏省挥发性有机物污染治理专项行动实施方案》
2017年底前,包装印刷、集装箱、交通工具、机械设备、人造板、家具、船舶制造等行业,全面使用低VOCs含量的涂料、胶黏剂、清洗剂、油墨替代原有的有机溶剂。集装箱制造行业在整箱抛(喷)砂、箱内外涂装、底架涂装和木地板涂装等工序全面使用水性等低VOCs含量涂料替代。交通工具制造行业使用高固体分、水性、粉末、无溶剂型等低VOCs含量涂料替代。家具制造行业使用水性、紫外光固化、高固体分等低VOCs含量涂料替代溶剂型涂料。机械设备、钢结构制造行业使用高固体分等低VOCs含量涂料替代。
《浙江省大气污染防治“十三五”规划》
推进工业涂装挥发性有机物污染综合整治。重点推进汽车制造、汽车维修、家具制造、船舶制造、工程机械制造、钢结构制造、卷材制造、电气机械制造等行业工业涂装工序挥发性有机物排放控制,深入实施《浙江省涂装行业挥发性有机物污染整治规范》。大力推广使用低(无)挥发性有机物含量的涂料和水性胶黏剂,限制使用即用状态下挥发性有机物含量>420克/升的涂料。优化涂装工艺,鼓励企业采用密闭型生产成套装置,推广应用自动连续化喷涂线。产生挥发性有机物污染物的涂装生产工艺装置或区域必须配备有效的废气收集系统,提高有机废气收集效率,提升末端治理水平。到2020年,工业涂装挥发性有机物排放量减少30%以上。
《山东省重点行业挥发性有机物专项治理方案》
提高低挥发性有机物含量的涂料使用比例。鼓励企业使用符合环保要求的水性、高固份、粉末、紫外光固化等低VOCs含量的涂料。降低单位产品的挥发性有机物排放量。鼓励企业采用静电喷涂、淋涂、辊涂、浸涂等涂装效率较高的涂装工艺,单位涂装面积的VOCs排放量应符合相关标准要求。
《上海市船舶工业涂装过程挥发性有机物控制技术指南》
采用环保型涂料(低VOC型涂料)或绿色涂料。对于溶剂性涂料应优先采用高固分涂料,即用涂料中VOCs溶剂含量在满足DB31/934标准要求的基础上,宜进一步控制在表1所示的水平。
对于部分仓室的内壁及部分构件宜考虑采用水性涂料。
应通过涂装工艺设计调整推广采用通用型底漆。
《广东省“十三五”挥发性有机物减排工作方案(征求意见稿)》
重点推进集装箱、汽车、家具、船舶、钢结构、其他交通运输设备等制造行业涂装过程的VOCs排放控制。到2020年,全省工业涂装VOCs排放量减少20%以上。
1集装箱制造行业
在整箱打砂、箱内涂装、箱外涂装、底架涂装和木地板涂装等工序全面使用符合标准要求水性涂料,到2017年,所有集装箱制造企业完成“油改水涂装线改造”。推广采用辊涂涂装工艺,加强废气收集与处理,严格执行行业VOCs治理自律公约,安装VOCs在线监测设备,确保废气排放稳定达标排放。
2汽车制造行业
推进整车制造、改装汽车制造、汽车零部件及配件制造等领域VOCs排放控制。推广使用高固体分、水性等低挥发性涂料,配套使用“三涂一烘”或“两涂一烘”等紧凑型涂装工艺;建立有机废气分类收集系统,整车制造企业有机废气收集率不低于90%,其他汽车制造企业不低于80%;对喷漆、流平、烘干等环节产生的废气,采取焚烧等末端治理措施,确保废气排放稳定达标排放。
3家具制造行业
重点针对木质家具制造大力推广使用水性、紫外光固化等低VOCs含量涂料,到2020年,替代比例达到60%以上;全面使用水性胶粘剂,到2020年替代比例达到100%。推广采用静电喷涂、淋涂、辊涂、浸涂等先进工艺技术。禁止无VOCs收集、净化措施的露天喷涂作业。加强废气收集与处理,对喷漆与烘干等环节产生的有机废气,采取焚烧等末端治理措施,确保废气排放稳定达标排放。
4船舶制造行业
船舶工业生产过程须控制涂料中VOCs的含量,对于机舱内部、上建内部等舱室的内壁宜采用水性涂料,对于溶剂型涂料应优先采用高固分涂料。船舶制造企业60%以上的涂装工作量须在封闭且带有排气净化系统的空间内进行;船舶修造企业的喷涂作业宜在局部封闭空间内进行并采取通风净化措施。推广使用高压无气喷涂、无气静电喷涂、空气辅助无气喷涂等高效涂装技术。
5钢结构制造行业
大力推广使用高固分涂料,试点推行水性涂料。推广使用高压无气喷涂、空气辅助无气喷涂、热喷涂等涂装技术,限制压缩空气喷涂的使用。逐步淘汰钢结构露天喷涂,建设废气收集与末端治理装置。
6其他交通运输设备制造行业
推广使用高固体分涂料,到2020年使用比例达到30%以上;试点推行水性涂料。积极采用机器人喷涂、静电喷涂等先进涂装技术。加强废气的收集与治理,对喷漆与烘干废气采用催化焚烧、蓄热焚烧等末端治理设施进行处理。
《浙江宁波涂装行业挥发性有机物污染治理技术指南(试行)》
推广使用环境友好型原辅料。根据涂装工艺的不同,鼓励使用粉末、水性、高固体份、紫外(UV)光固化涂料等环境友好型涂料,鼓励使用即用状态下VOCs含量≤420g/L的涂料,从工艺的源头减少原辅材料的VOCs含量,实现VOCs减排目的。
从以上各地方政府发布的政策来看,其更多的是从涂装领域及细分行业入手,针对性的提出减排的方法,从终端角度倒逼涂料企业必须注重绿色涂料的研发与生产,降低VOC的排放。在已发布的文件中,并没有支持“禁油令”的说法出现,解读为“限油令”更合适些,其中的“油”应理解为涂料中的挥发性溶剂,而不是针对油性涂料本身。
说回水性涂料,按GB/T 5206—2015中2.274,其定义是“挥发物的主要成分为水的一类涂料”。实际上水性工业涂料中还是含有部分VOC的,从已经发布的一些有害物质限量标准中可以看出,如HJ 2537-2014 《环境标志产品技术要求 水性涂料》。
作为防腐涂料的未来绿色化,水性是很好的一个方向。 HG/T 5176-2017《钢结构用水性防腐涂料》也即将发布,其适用于以水为主要分散介质、在大气腐蚀环境(C2~C4)条件下使用的低合金碳钢材质的钢结构表面用防腐涂料。但其中也特别说明,本标准不适用于浸泡、埋地、储罐衬里等腐蚀环境以及很高腐蚀性的大气腐蚀环境(C5-I和C5-M)下使用的钢结构。如果在没有解决现阶段水性涂料施工性、涂膜性能的限制下将其用在重防腐环境,或许只会起到适得其反的效果,最终将是对水性涂料的“捧杀”,因为对于业主来说,其关注的只是最终防腐效果,而在国内很多施工队并不专业的情况下,原本难得的防腐效果又会大打折扣。
除了水性涂料,我们还应该去特别关注高固体分、无溶剂涂料。现实的情况是,大部分的防腐涂料企业都是油性为主,其技术力量以及生产线改为生产高固体分、无溶剂涂料并没有太大的压力;对于使用普通溶剂型涂料的涂装企业来说,在不需要大规模改造的情况下,就可以用高固体分涂料取代现有的普通防腐涂料,这是最容易达到的“降本增效”的选择。
网络上“禁油令”字眼的出现,也许是为了推进水性涂料的发展,但其不分行业、不分环境的一刀切,其实不管是对溶剂型涂料,还是对水性涂料都是一种伤害。因为,这两类涂料都是有自身特点以及优劣势的,在防腐领域,我们希望可以客观的去对待水性、高固体分、无溶剂涂料,将其放在同样的关注度上。保证在不降低现有溶剂型涂料性能的情况下,充分降低VOC排放,才是我们最需要关注的问题。就像此次防腐涂料年会的主题二与主题三,水性涂料,现在需要进行的是提高产品性能、降低涂装要求;高固体分、无溶剂涂料则是涂料涂装企业的低成本的绿色转型之路。
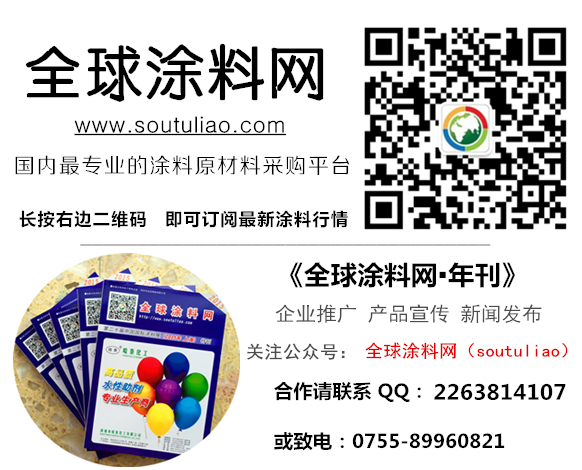
热点资讯
|
|